Since I’ve recently been doing some work around maintenance plans, I thought this could be a good topic for a few blog post.
First you must setup the category for the maintenance plan. I recommend creating a new category and then following the remainder of this section to complete all the needed configuration.
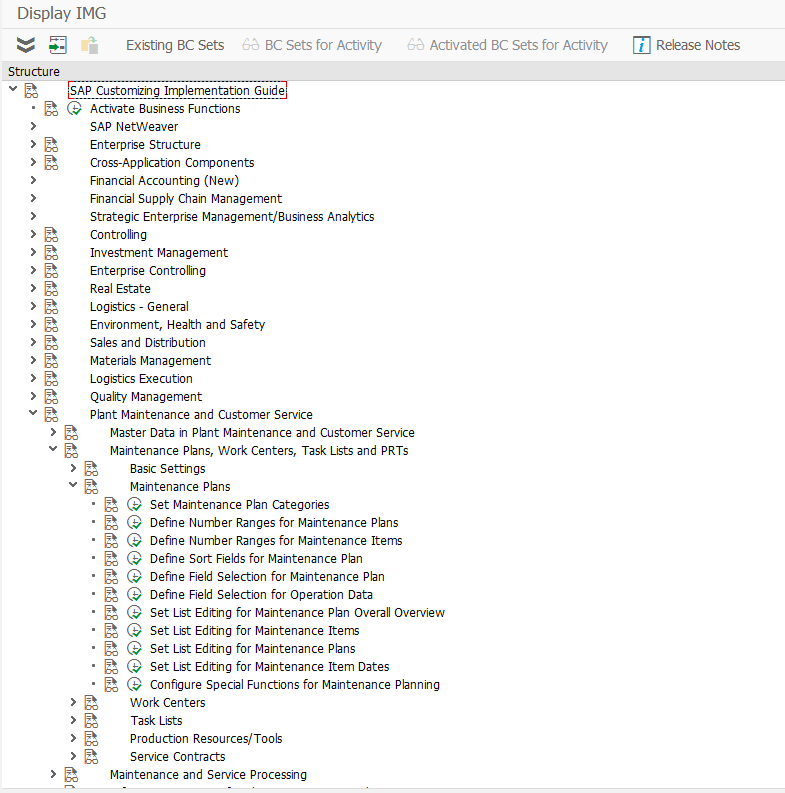
IMG->Plant Maintenance and Customer Service-> Maintenance Plans, Work Centers, Task Lists and PRTs -> Maintenance Plans -> Set Maintenance Plan Categories
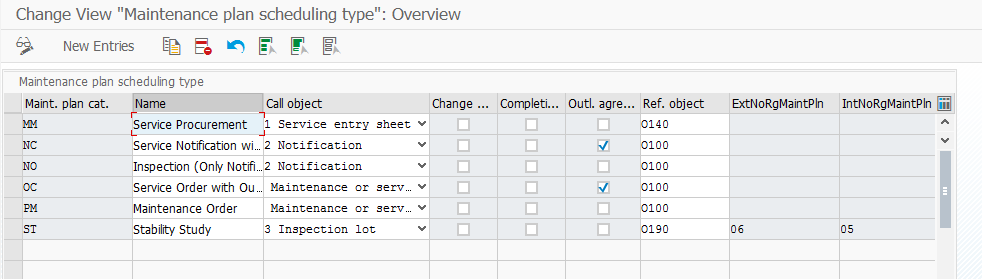
Click on new entries to create your own version.
Maint. Plan cat. : This is the 2 digit category for your maintenance plan type. It is recommended to create a different category for each major category.
Name : This is just the description of the category.
Call object : This is the type of document that will be generated by the plan. Keep in mind, depending on your process, you may select a “softer” document like the notification to put a reminder out to the call center to contact a customer to setup an appointment. Or you may need a “harder” document that say on Nov 15th, a technician must be on-site to perform yearly maintenance. This will often depend on your agreement with the customer.
Service Entry Sheet
Notification
Inspection Lot
Maintenance or Service Order
In service, the most common selections will be Notification or Service Order.
Change Documents: Do you want to collect change documents for any changes that you make to the plan. I’m a big fan of history, so I always encourage this to be checked. You never know when you might need it.
Completion Data: You can use this indicator to influence the maintenance processing process. For example, you can prevent that every employee who can complete orders and notifications can also influence the scheduling of maintenance plans through the data.
With this indicator you can:
Activate a separate completion for the maintenance plan for the completion of call object notification and order.
Activate a dialog for the completion of notifications and orders using list processing.
Activate additional functionality for completing the call objects notification and order using a BAdI.
If you select the indicator completion date, you can enter a reference time that only applies to the maintenance plan, when you are completing a call object (notification or order) generated from a maintenance plan. To do this, you can also use the maintenance-plan-based fields completion date and completion time when you are completing an order or a notification.
These fields are pre-filled with the original plan date and the current time. If the current system date is displayed, then the original plan date is in the future and is replaced by the system date.
This is functionality I have not used in the past.
Outline Agreement: Should this be created with reference to an outline agreement. If you want to create a plan with reference to a service contract, this must be checked.
Ref Obj: This defines the type of object that the plan will “work” on.
O100 Functional location+equipment+assembly
O110 Equipment + assembly
O120 Functional location(30)+equipment+assbly
O130 Serial number+material number+device ID
O140 Without reference object
O150 Equipment only
O160 Functional location only
O170 Equipment + Serial No. + Material No.
O180 Functional loc. 1:1 + equip. + assembly
O190 Physical sample
You might recognize this list from the notification defaults. I tend to always select O170.
Something interesting to take note of. In my ECC 6.0 EHP4 system, in transaction IP50, the last category with the Outline agreement checked does NOT show up. In my EHP7 system, this doesn’t happen. I could not find anything in OSS that directly corrects this. A workaround would be to create an addition plan 00 or ZZ or something with the description of do not use. Then the previously created plan should show up just fine.
Thanks for reading,